This article dives deep into the world of Medium-Density Fiberboard (MDF) and Particle Board (also known as chipboard), two of the most popular engineered wood products used in furniture manufacturing, interior design, and construction. Understanding the differences between these materials is crucial for making informed decisions, ensuring you choose the right product for your specific needs, whether you’re a furniture manufacturer, a cabinet maker, or a DIY enthusiast. This guide will provide you with comprehensive knowledge, empowering you to choose between MDF and particle board with confidence.
1. What Exactly are MDF and Particle Board?
Both Medium-Density Fiberboard (MDF) and Particle Board (often referred to as chipboard) are engineered wood products. This means they are manufactured by combining wood byproducts, such as wood fibers, wood chips, sawdust, and shavings, with a synthetic resin adhesive and then compressing them under high heat and pressure. This process creates a dense, stable, and uniform panel that is often used as a substitute for solid wood in various applications. However, the specific manufacturing processes and the types of wood byproducts used create key differences in their properties. MDF generally uses finer wood fibers, resulting in a smoother and denser product, compared to particleboard, which uses coarser wood particles.
MDF and particleboard are frequently chosen for their cost-effectiveness, versatility, and dimensional stability. They don’t warp or crack like natural wood can, making them ideal for furniture, cabinetry, and interior finishes. However, their differences in density, strength, and moisture resistance make each material better suited for specific applications.
2. How is MDF Manufactured? A Deep Dive into the Process
The manufacturing process of MDF starts with breaking down hardwood or softwood residuals into fine wood fibers, often using a defibrator. These fibers are then combined with a wax and a resin binder, typically a urea-formaldehyde or other formaldehyde-based adhesive. This mixture is then formed into a mat and subjected to a hot press, where high temperature and pressure bond the fibers together, creating a dense and homogeneous panel. After pressing, the MDF board is cooled, sanded to achieve a uniform thickness and a very smooth surface, and then cut into various sizes.
The key to MDF’s quality is the consistency of the wood fibers and the even distribution of the resin. This results in a panel with no voids or knots, making it ideal for intricate machining and finishing. The use of fine fibers also contributes to MDF’s superior screw-holding ability compared to particleboard.
3. Particle Board Production: From Wood Chips to Finished Panel
Particleboard (chipboard) is manufactured by mixing wood chips, planer shavings, or sawdust with a synthetic resin, usually urea-formaldehyde. This mixture is then spread into a mat, often in a three-layer particleboard structure with finer particles on the surfaces and coarser particles in the core. This mat is then compressed under high heat and pressure in a hot press to form a rigid panel. The panel is then cooled, sanded, and cut to size.
The type of wood particles used, their size, and the resin type all affect the final properties of the particleboard. Higher-density particle board uses smaller particles and more resin, resulting in a stronger and more stable product. While particleboard is generally less expensive than MDF, its coarser texture makes it less suitable for applications requiring a very smooth finish or intricate detailing.
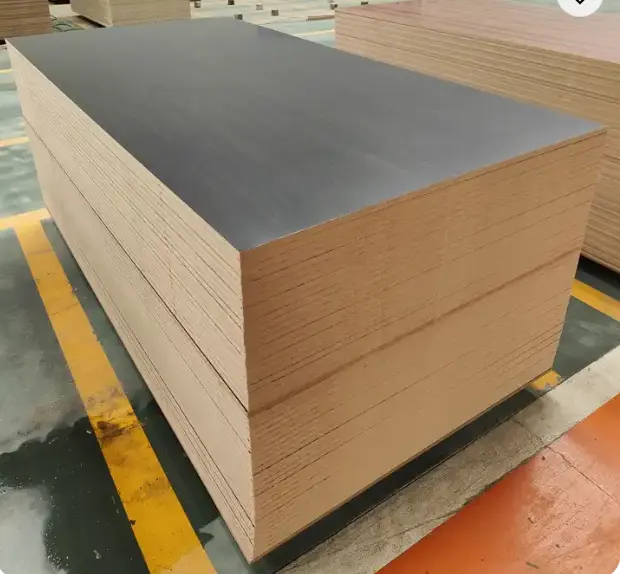
4. MDF vs. Particle Board: Density and Strength Showdown
MDF, or Medium-Density Fiberboard, as the name suggests, has a higher density than particle board. This higher-density translates to greater strength and a more solid feel. MDF’s density typically ranges from 600 to 800 kg/m³, while particleboard’s density can range from 160 kg/m³ to 450 kg/m³ for standard grades and up to 720 kg/m3 for high density board. This difference in density is a direct result of the size and type of wood particles used and the amount of resin used in the manufacturing process.
Because of its greater strength, MDF is less prone to damage during handling and machining. It also offers better screw-holding power, making it a preferred choice for furniture and cabinetry where strong joints are essential. Particleboard, while still strong enough for many applications, is more susceptible to chipping and damage, especially at the edges. A thicker particle board, however will increase it’s strength.
5. Surface Finish and Workability: Which is Easier to Use?
One of the most significant advantages of MDF is its exceptionally smooth surface. This is due to the fine wood fibers used in its production. This smooth finish makes MDF ideal for painting, laminating, and applying veneer. It provides an excellent substrate for a flawless finish, with no need for extensive sanding or filling.
Particleboard, on the other hand, has a coarser surface due to the larger wood particles used. While it can be sanded smooth, it typically requires more effort and may still not achieve the same level of smoothness as MDF. This makes particleboard less ideal for applications where a high-quality painted finish is required. However, when covered with paint or another sealer or laminate, like melamine, the surface difference becomes less of a concern. For an example of melamine covered particle board, see Melamine Particle Board Double Sides White.
6. Moisture Resistance: A Critical Factor for Longevity
Neither MDF nor standard particleboard is inherently resistant to moisture. Exposure to water or high humidity can cause both materials to swell, warp, and lose strength. The edges of both are particular prone to damage. This is a significant limitation, especially in areas like kitchens and bathrooms.
However, moisture-resistant grades of both MDF and particleboard are available. These specialized boards are manufactured using moisture-resistant resins, such as melamine-urea-formaldehyde or phenolic resin, and are designed to withstand occasional exposure to moisture. It’s crucial to specify moisture-resistant boards for applications where humidity or water contact is a concern. Remember that even moisture-resistant grades are not waterproof and prolonged exposure to water should be avoided. If looking for moisture-resistant material, it’s important to consider the level of formaldehyde present in the resins.
7. Cost Comparison: MDF vs. Particle Board – Balancing Quality and Budget
Particleboard is generally the least expensive of the two options. Its lower cost is primarily due to the use of cheaper wood chips and waste products as raw materials. This makes particleboard a popular choice for applications where budget is a primary concern, such as for the concealed parts of furniture or for subflooring.
MDF, while more expensive than particleboard, is still a cost-effective alternative to solid wood. The higher cost of MDF is justified by its superior strength, smooth surface, and workability. When considering the overall cost, it’s important to factor in the potential for reduced labor costs due to MDF’s ease of finishing and machining.
8. Applications: Where is MDF the Best Choice?
MDF’s superior properties make it the preferred choice for a wide range of applications, including:
- Furniture: MDF’s smooth surface and ability to hold intricate details make it ideal for painted furniture, furniture with veneer finishes, and furniture components that require precise machining.
- Cabinetry: MDF is often used in furniture and cabinetry, particularly for doors and drawer fronts, where a smooth, painted finish is desired.
- Interior Trim and Moulding: MDF’s stability and ability to be shaped into intricate profiles make it a popular choice for baseboards, crown molding, and other decorative trim.
- Speaker Boxes: MDF’s density and acoustic properties make it a common material for speaker enclosures.
- Door Manufacturing: Certain types of doors benefit from the density and smooth finish of MDF. See this example of melamine impregnated paper for MDF.
9. When Should You Choose Particle Board (Chipboard)?
While MDF has many advantages, particleboard (chipboard) remains a viable option for specific applications, particularly where cost is a major factor:
- Concealed Furniture Components: Particleboard is mostly used for making furniture, it is often used for the internal, unseen parts of furniture, such as the back panels of cabinets or the bottoms of drawers.
- Shelving: For inexpensive shelving units, particleboard provides a cost-effective solution, especially when covered with a laminate or veneer.
- Subflooring: In some construction applications, particleboard can be used as a subfloor material, providing a stable base for flooring finishes.
- Office furniture: Often used for backing or sides of desks.
- Underlayment: Particleboard can serve as an underlayment for floor coverings, providing a smooth and level surface.
10. Formaldehyde Emissions: Understanding the Health and Safety Aspects
One of the key concerns with both MDF and particleboard is the potential for formaldehyde emissions. Urea-formaldehyde resin, a common binder used in both materials, can release formaldehyde gas over time. Formaldehyde is a known human carcinogen, and exposure to high levels can cause respiratory irritation and other health problems.
Regulations, such as CARB P2 (California Air Resources Board Phase 2) and E1/E0 formaldehyde emission standards, limit the amount of formaldehyde that can be released from composite wood products. Choosing products that comply with these standards is crucial for ensuring indoor air quality and protecting the health of occupants. Always ask your supplier about the formaldehyde emission levels of their products. Reputable manufacturers, especially those exporting to the USA, North America, Europe, and Australia, will adhere to these stringent standards.
11. Sustainability Considerations: Environmental Impact of MDF and Particle Board
Both MDF and particleboard can be considered relatively sustainable materials, as they are made from waste wood products that might otherwise be discarded. This utilization of waste products helps to reduce the demand for virgin timber. However, the sustainability of these materials also depends on the source of the wood and the manufacturing processes used.
Look for products that are certified by organizations like the Forest Stewardship Council (FSC), which ensures that the wood comes from responsibly managed forests. Also, consider the formaldehyde emission levels, as lower emissions generally indicate a more environmentally friendly product. Choosing a supplier that prioritizes sustainable practices is essential for minimizing the environmental impact of your project.
12. Choosing the Right Supplier: Partnering with a Reliable Manufacturer
Selecting the right supplier is crucial for ensuring you receive high-quality MDF or particleboard that meets your specific requirements. Here are some key factors to consider:
- Quality Control: A reputable supplier will have rigorous quality control procedures in place to ensure consistent product quality, including checks for density, surface finish, dimensional accuracy, and lamination quality (for melamine boards).
- Certifications: Look for suppliers who can provide products that meet relevant industry standards, such as CARB P2, E1/E0, and FSC certifications.
- Product Range: A good supplier will offer a wide range of thicknesses, sizes, and finishes to meet your diverse needs. An example of various finishes can be found on this page.
- Logistics and Delivery: Ensure the supplier has efficient logistics and delivery capabilities to meet your project timelines. This is a common pain point for purchasers like Mark Thompson.
- Communication: Choose a supplier who is responsive and provides clear and timely communication. Allen, with his direct factory experience, can be a good resource. Inefficient communication is a major concern for many buyers.
- Experience in Exporting: If you are in the USA, North America, Europe, or Australia, find a supplier, like Allen, that has experience exporting to those regions.
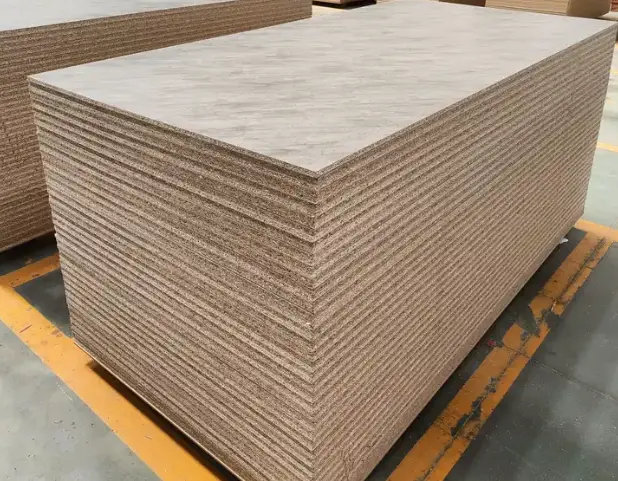
A Note from Allen:
As a factory owner in China with multiple production lines specializing in wood-based panel products and decorative materials, I, Allen, understand the needs of international buyers like Mark Thompson. My company, Demeter, focuses on producing high-quality RAW MDF, MELAMINE FACED BOARD, MELAMINE PAPERS, PRINTED PAPER, BASE PAPER, and EDGE BANDING. We prioritize quality control, adhere to international standards (CARB P2, E1/E0), and offer competitive pricing. Our main export markets include the USA, North America, Europe, and Australia. We understand the importance of efficient communication, timely delivery, and providing detailed product information, addressing the common pain points experienced by procurement officers. We regularly attend exhibitions to showcase our products and connect with potential customers.

Summary: Key Takeaways
- MDF and particle board (chipboard) are both engineered wood products made from wood byproducts and resin.
- MDF uses finer wood fibers than particleboard, resulting in a denser and smoother product.
- MDF is generally stronger and more workable than particleboard.
- Particleboard is typically more affordable than MDF.
- Both materials are susceptible to moisture damage, but moisture-resistant grades are available.
- Formaldehyde emissions are a concern, so choose products that meet relevant standards (CARB P2, E1/E0).
- Consider the sustainability of the materials and choose suppliers who prioritize responsible sourcing and manufacturing.
- Careful supplier selection is crucial for ensuring product quality, timely delivery, and clear communication.
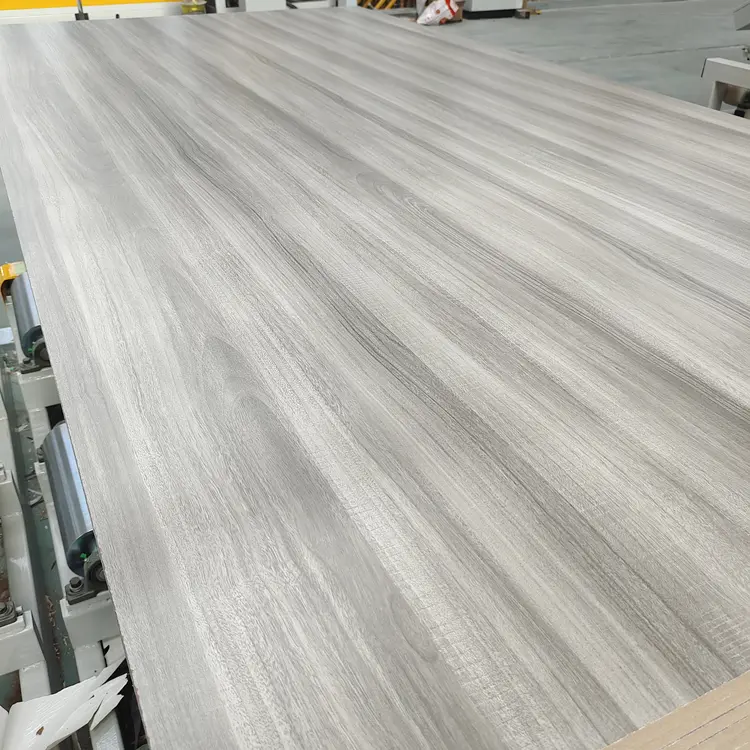
Post time: 03-18-2025